※MP-Connect(エムピイコネクト)はパナソニック ホールディングス株式会社の登録商標です。
MP-Connectとは
MP-Connectは、DX化でお悩みの経営者・現場担当者様の課題に応えるMESソリューションです。
“モノづくりの現場力を活かし、現場を育てる”をテーマに、お客様自身で現場の変化に合わせたシステムの変更が可能です。
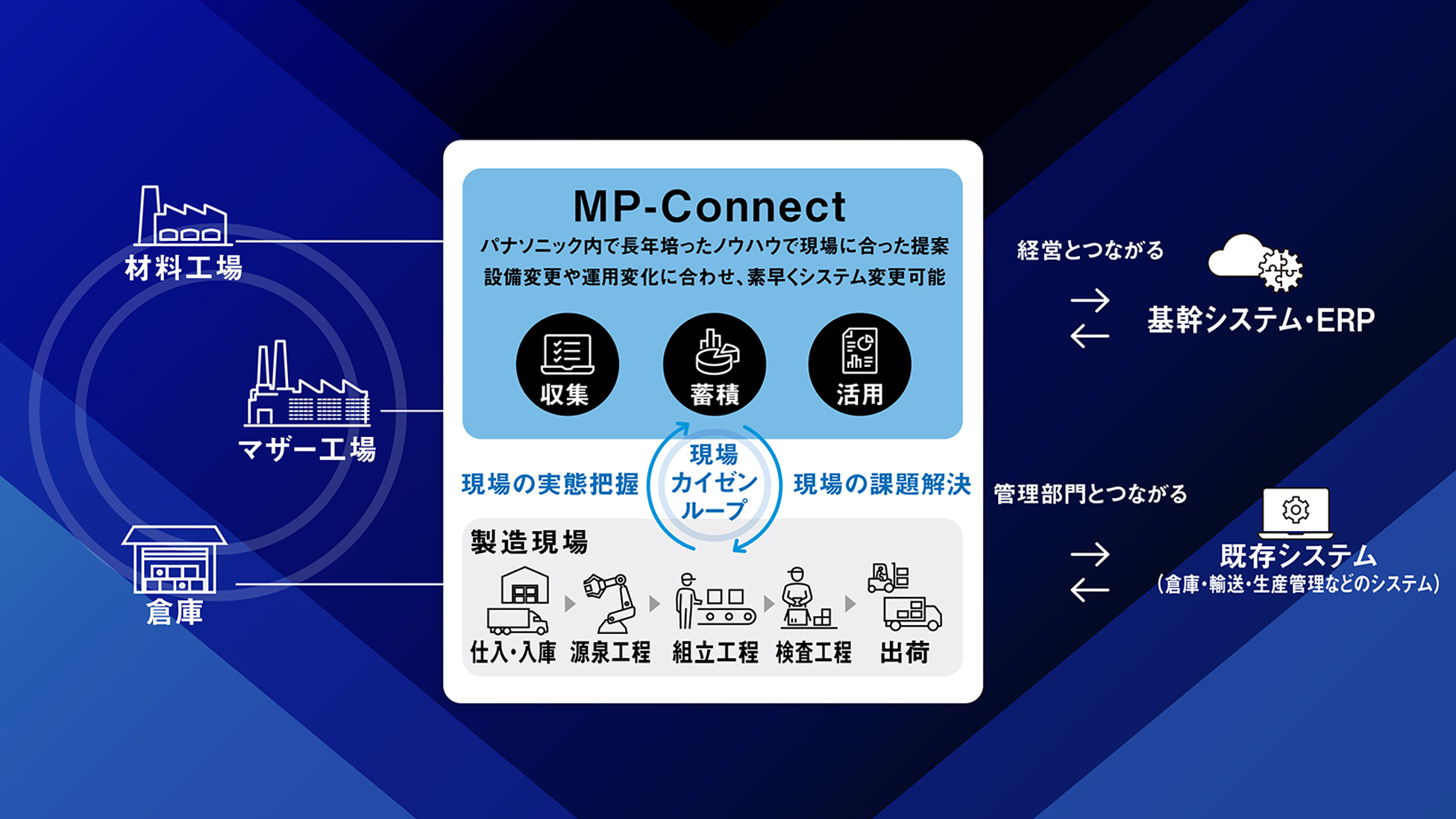

生産現場の課題
自動ライン(デバイス系)
- 1品ごとに大量のデータを収集し解析したいが、欠損なく収集・蓄積が困難
- 大量生産のため異常発生時の発見遅延が大量の不良品につながる
人による組立作業(セット系)
- 人の生産性は、作業や場所が多様なため、生産数や品質のデータ化が難しい
- 現場運用やレイアウトなど頻繁に変わるため、システムの変更に時間と費用がかかる
単体装置(加工・混合系)
- 設備メーカによりインターフェイス仕様が異なるため、データを吸い上げる仕組みがなく、解析しずらい
- 液体や粉体のため、材料ロットのトレーサビリティが難しい

経営者・現場担当者の課題
経営視点
- 費用対効果が見えない
- どんなシステムを導入していいかわからない
- DXを推進するために何をすればよいかわからない
- DX化に対応できる人材がいない
現場視点
- 普段の業務で手一杯
- 部門間で連携できない
- つねに経営効果を問われる
- 運用変化に追従できずにシステム利用が定着しない
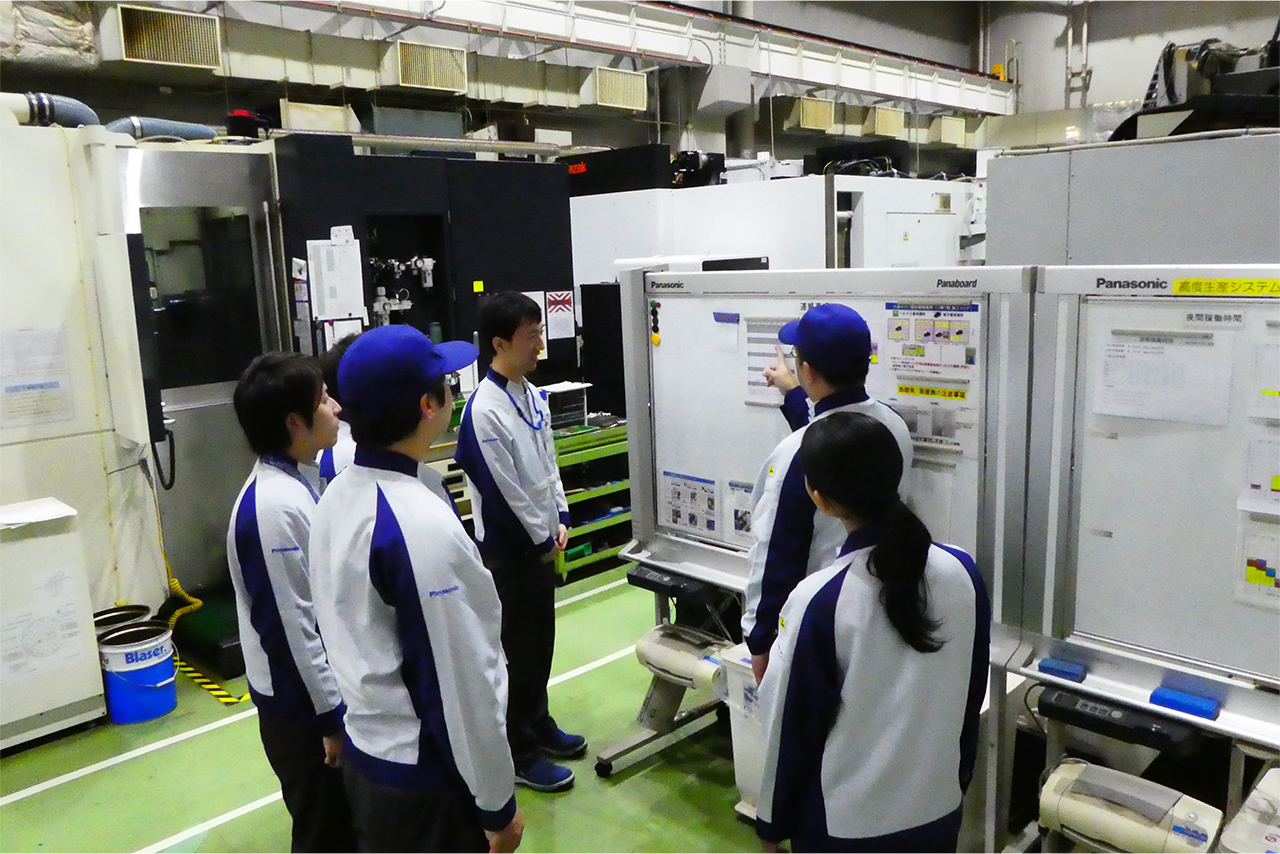
課題に対するご提案
現場の課題を抽出
現場の状況を客観的に把握し、経営・現場視点でお客様と共に課題を抽出します
部門間、設備メーカー、ITベンダーとの調整
- 部門によって、システムの導入目的や範囲などが異なる場合、調整を行い同じゴールへ導きます
- 設備メーカーやITベンダーなど、言葉の壁も理解し、調整を行います
設置機器選定
お客様の現場に合わせ、最適な機器を選定します

MP-Connectの特徴
「設備・工程・システム・ノウハウ・工場」の
“あらゆるデータがつながる生産現場”を実現し、
“現場カイゼン” に貢献します。
お客様のモノづくりノウハウと
30年以上のパナソニックMES導入経験の融合
現場や経営のスタイルに合わせ最適提案。 まずは、現場の見える化からスタート。 データの収集・活用を行い、現場に合わせて ステップアップ導入できます。
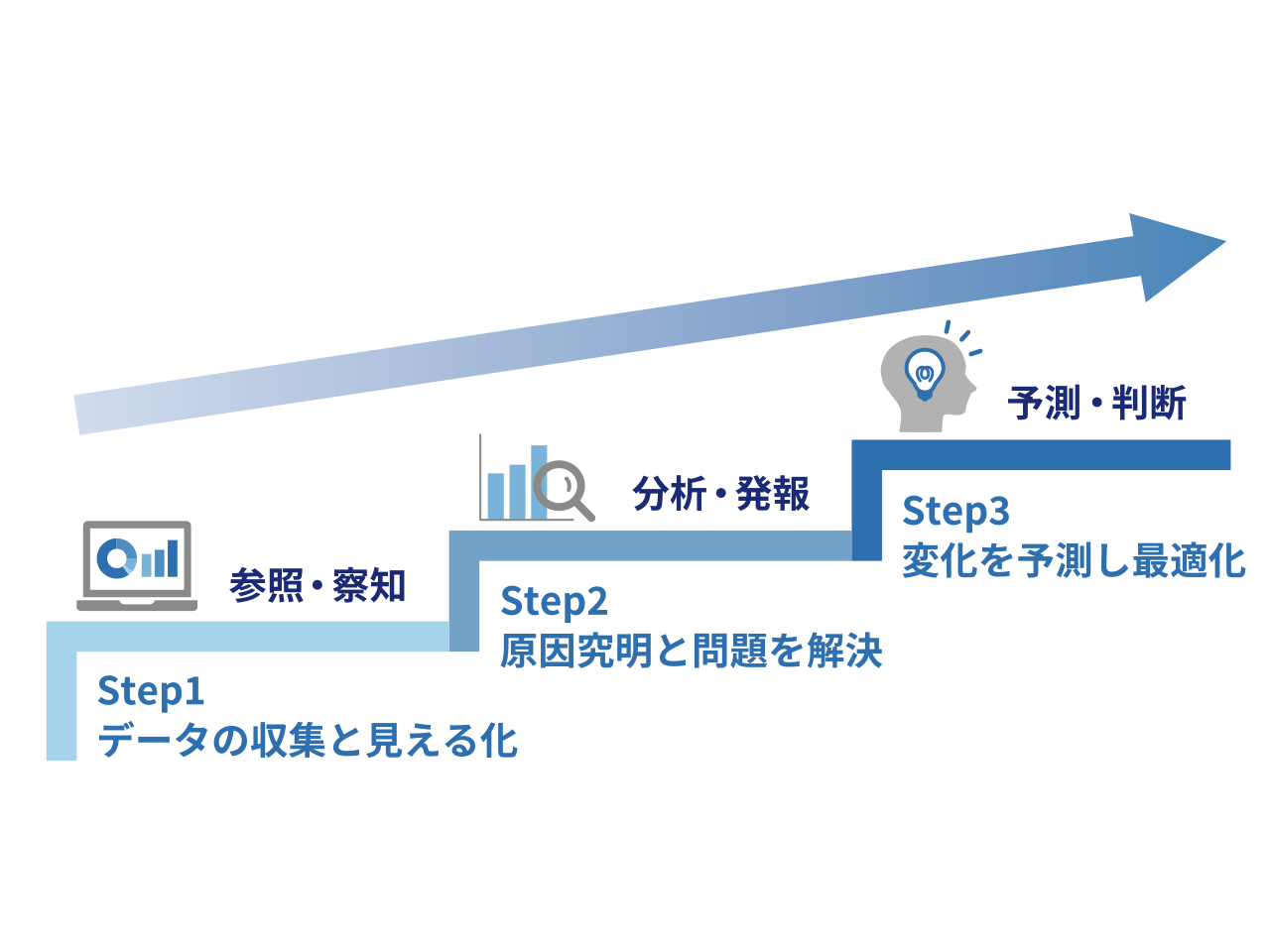
設備変更や運用変化に合わせ、
素早く変更可能なシステム
老朽化に伴う設備入れ替えや、 生産機種の変更・省人化などによる運用変化に対応。 「ここを確認したい」「少しだけ変更したい」を、 お客様自身で実現できます。
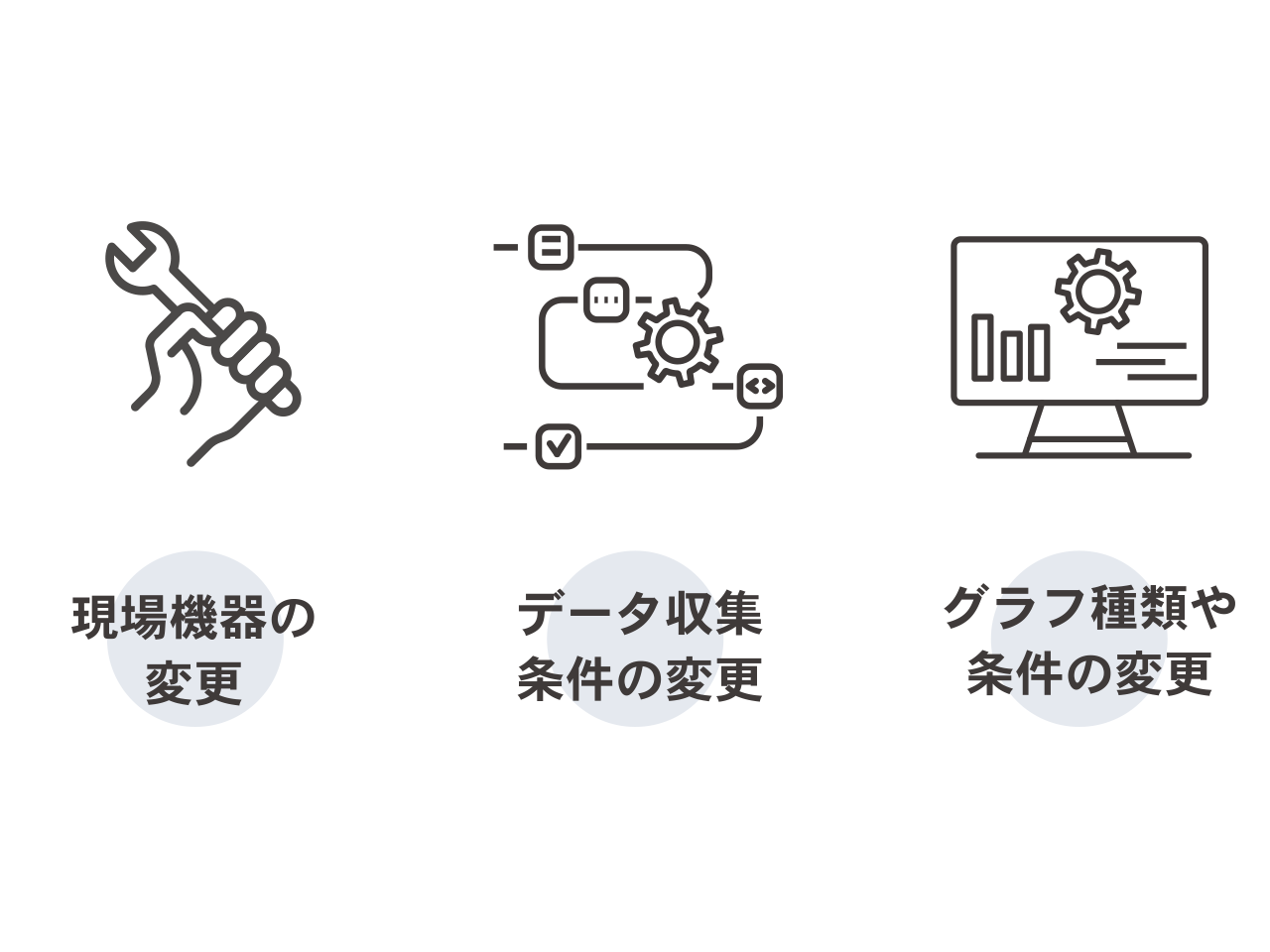
導入事例
事例1.設備監視&発報(A社導入)
課題:
人が設備状態を1時間ごとにチェックしていたため、
異常に気付くのが遅れ、品質不良となる問題があった。
改善内容:
1. 設備データを収集・自動集計
2. 現在情報を監視モニタに表示
3. 異常発生時は設備と担当者へ発報
結果:
人による監視業務が不要になり、蓄積されたデータを活用することで品質不良を未然に防ぐことができるようになった。
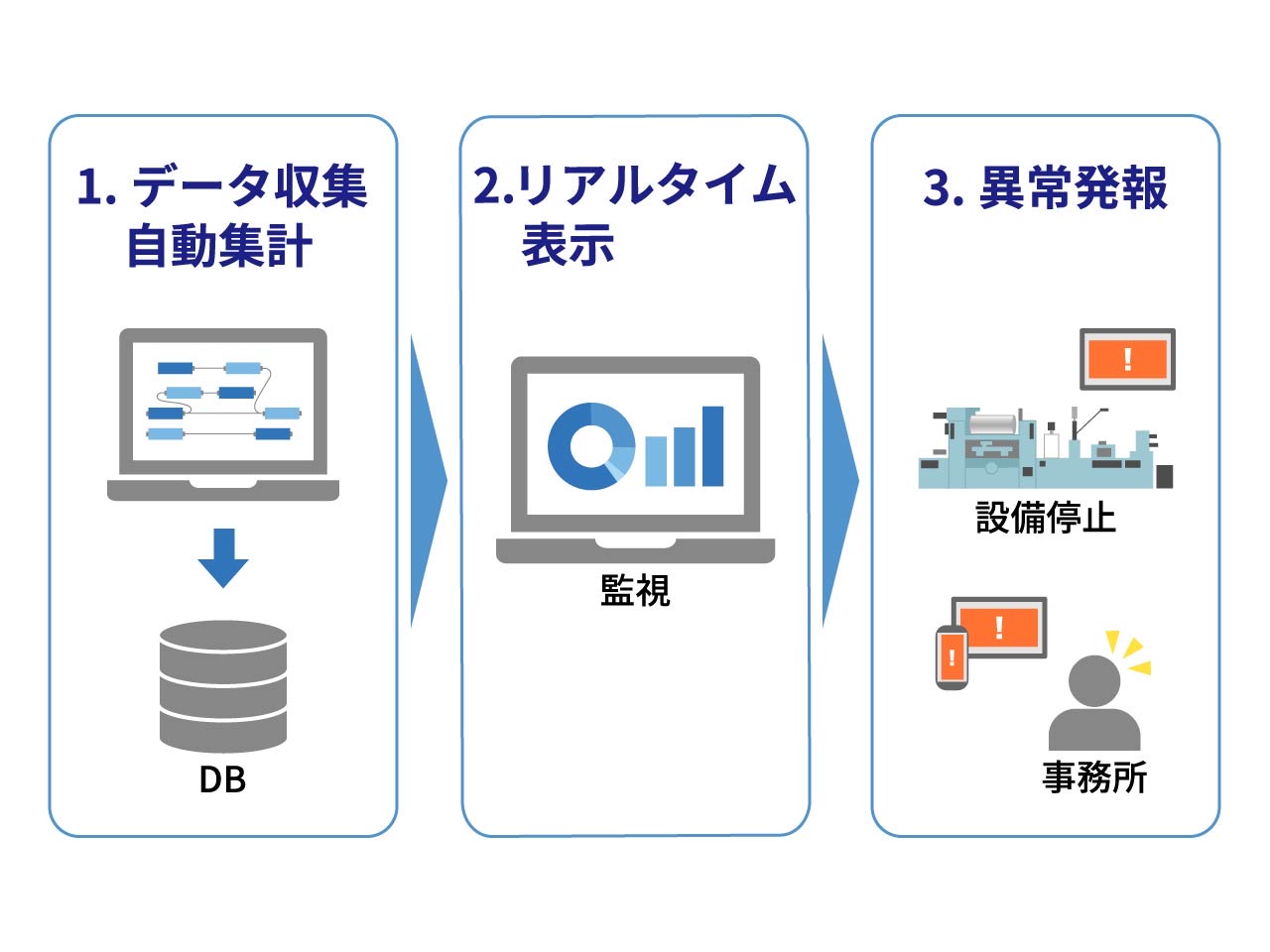
事例2.材料供給予測(B社導入)
課題:
材料切れが起こるたびに、生産が止まっていた。
改善内容:
1. 消費データから在庫計算
2. 材料切れ時刻を予測
3. 最適タイミングで搬送指示
結果:
搬送の前段取りかができることで、停止時間が削減され、生産性が向上した。
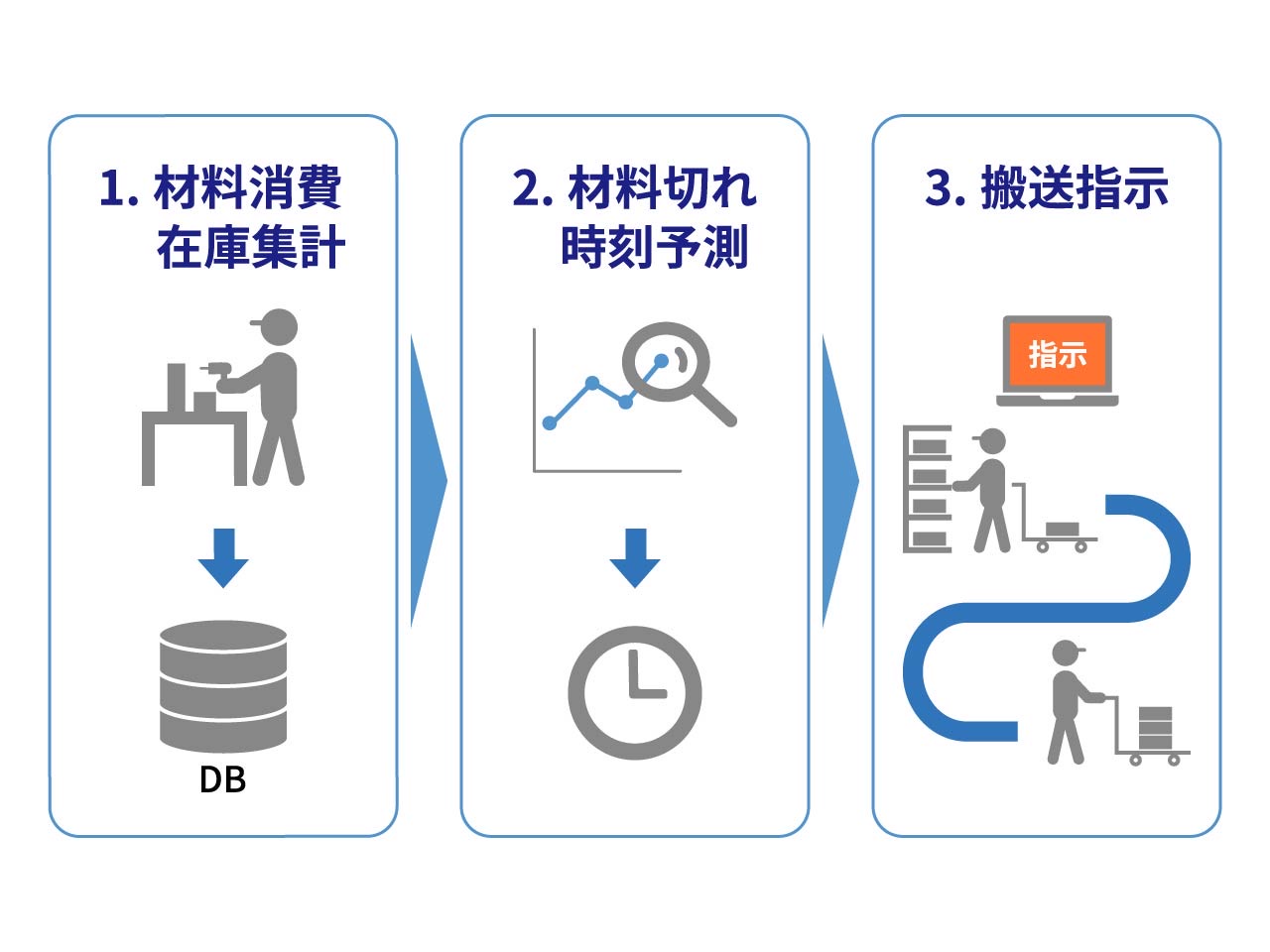