Alternative materials
A Natural Alternative To Plastic
Not only in energy generation, but also in production itself, fossil fuels need to be eliminated. Plastic is a miracle material: cheap, durable, flexible, and producible in thousands of shapes and colours.
But its best qualities can also provide drawbacks when not properly recycled. Every year, more than 300 million tons of plastic waste are produced worldwide, half of which is destined for single use. In the end, only 9% of all plastics are recycled.
Therefore, other more sustainable materials may replace plastics in certain uses cases. Since 2015, Panasonic scientists and engineers have been researching on innovative materials. based on plant fibres, or more precisely cellulose. For this purpose, wood and even wood waste or plant-based industrial waste is used.
The cell walls of plants consist largely of cellulose. Chemically nothing more than sugar, cellulose is the most abundant biomolecule in nature. Its long molecular chains assemble into larger structures to form tear-resistant fibres that give plants their stability. By mixing the cellulose fibres with resins, Panasonic later recycles through its recycling processes, creating a closed loop of recyclable materials.
Usually, the production of cellulose requires a great deal of fresh water. The individual fibres are obtained by grinding them in water, but before they are mixed with resins, they must first be dried by machine. This process costs time, water and energy.
In contract to that, the method developed by Panasonic is a process that works in a completely dry environment without water. This production method not only saves water but also energy, which results in saving 1.8 kg of CO2 per kg of cellulose.

For the first time in a household appliance, Panasonic has used cellulose fibre in the Japanese market. The strong, flexible and lightweight moulded material made from plant matter, forms part of the housing for the MC-SBU820J/MC-SBU620 cordless upright vacuum cleaner (introduced in 2018). The sustainable fibre has approximately eight times the impact strength of fiberglass. It makes the product more durable while reducing the amount of conventional plastic which would normally be processed.
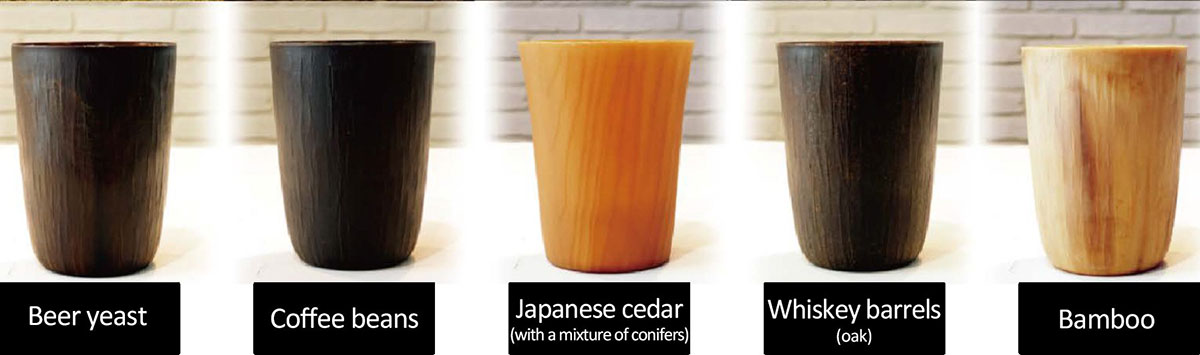
The second use case is in the food industry. In collaboration with the Japanese brewery, Asahi, Panasonic developed a reusable cup for drinking beer, called the „forest tumbler“.
The Future Of Sustainable Plastic From Plants
Demand for sustainable materials is growing in all industries. Panasonic has worked hard to improve the strength and durability of plant-based moulding material and increase the concentration of cellulose fibres. Similarly, the manufacturer is developing variants with different material properties that are suitable for a wide range of applications.
Related sustainable manufacturing topics
The avoidance of pollutants in the production process
With the aim of protecting the environment and its customers, Panasonic has developed and implemented its own management system for chemical substances in products, with chemical substances managed throughout the global supply chain, production and use of products.
For more information, please contact
Panasonic Europe B.V
Corporate Communications