History of Battery Development
An outline of the major products that shaped our history, including a number of notable events from SANYO, a company Panasonic acquired in 2010.
1923
Development and release of
battery-powered shell lamps
In March 1923, Konosuke Matsushita, founder of the business that would later become Panasonic, successfully developed a cannonball-shaped battery-powered shell lamp for bicycles. It was a breakthrough product. A special battery assembly method and new bulb-type lamp were used to provide 30 hours of operation, where two to three hours was average for similar products at the time.

Released the Excel Dry Battery to suit shell lamps
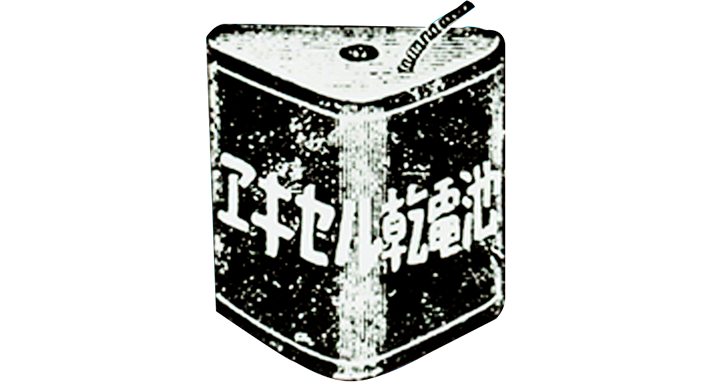
1927
First National-brand square-shaped lamps released
For application beyond the cycle market, Mr. Matsushita invented a square-type handheld lamp in 1927. It was the first product to be marketed under the name National. Despite tough economic times during the 1930s, annual lamp production surpassed six million units. This major hit led to a spike in battery sales. To cope with demand, Matsushita Electric Factory (as it was now known) took over the Komori Battery Factory in September 1931 and commenced in-house battery production. Following that, in 1932, the company took over Okada Battery Company’s Tsujido factory and opened the Kadoma Battery Factory soon after. A new factory in the Sangou area followed in 1933 and since 1935 the site has served as the home of our battery business. As well as the successful lamp products, battery sales shot up to three million units and contributed to Matsushita Electric’s development.
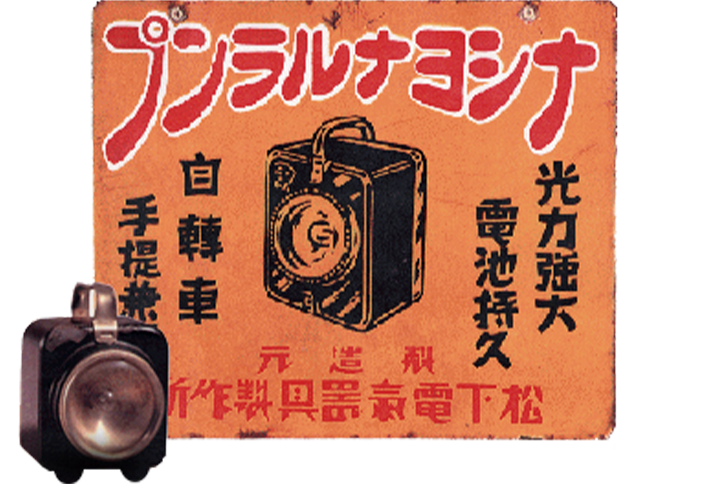
1931
Started in-house production of dry batteries and introduced National battery for the square lamp
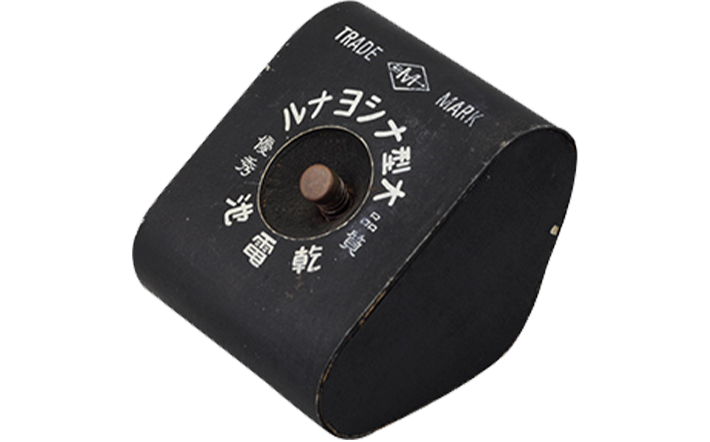
1937
Released automotive lead-acid batteries
The company started development of a rechargeable battery for civil applications from 1935 to 1944, shifting to military supply during wartime. Production was mainly geared towards the automotive market, but lead-acid technology also found application on bicycles in the form of the Ever Light. New rechargeable batteries followed with portable lamps, a fish-collecting lamp, and stationary-rechargeable batteries using Tudor-type plate (a kind of plate for lead-acid batteries) entering production. To improve quality control, lead powder production was moved in-house. Okada Battery Company specialized in dry batteries rather than lead-acid types, so Matsushita Electric placed research under the leadership of Professor Yokoyama of Yokohama Engineering High School (now Yokohama National University). Staff conducted research in a test-production factory that was, by today’s standards, primitive. The first trial lead-acid battery was the automobile AR5-6 type. The A signifies automobile, R stands for the rubber used for the battery container, 5 denotes the number of negative plates, and 6 represents 6 Volts. The factory was later appropriated for military use and independent research and development was suspended.

1940
Air-dry batteries released
1941
Carbon-grounding rods developed and released
1942
Air-wet batteries make debut
1945
Laminated-dry batteries released
1954
Released National Hyper, the first full-metal-jacket dry battery in Japan
The outbreak of the Korean War in 1950 drove demand and revitalized the industry. Technical tie-ups and cooperation with overseas manufacturers also became popular. Sticking to the policy of having “persistence to develop a world-class product with our own technology,” all the raw materials and parts were made in-house to ensure consistent quality. The National Hyper, the first full-metal-jacket dry battery in Japan, was successfully introduced in April 1954. With this release, National batteries gained a stronger foothold. A number of other products were also developed in conjunction with batteries, including flashlights and lamps (which were in high demand), as well as gas lighters and new products such as battery-powered clocks, automatic gas stoves, emergency-call buzzers, and bath buzzers. New markets in heating, energy, and audio were opened, and battery demand started to expand rapidly, leading to the full automation of production.
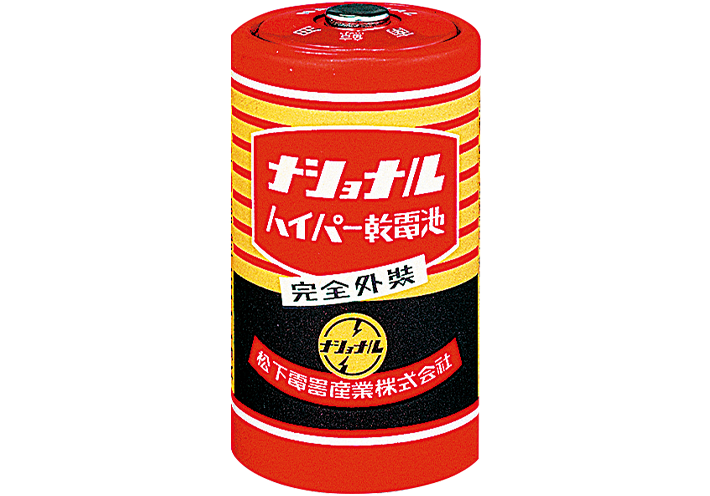
1963
Released National Hi-Top manganese dry batteries
Right after the release of the National Hyper battery, management realized that the scope of application was being limited by performance. It was decided that a battery with twice the shelf life of conventional designs should be developed. Within the size limitations imposed by international standards, overcoming difficulties concerning chemical compositions proved to be a great challenge. The objective was to create a battery that was less likely to leak, that wouldn’t self-discharge, and that would deliver high performance in heat, cold, and humidity. Finally, in 1963, Matsushita Electric succeeded in developing the Hi-Top, a battery with double the shelf life of existing models. The battery was used in wide range of appliances such as electric shavers and calculators, and demand increased yet again. Matsushita Electric continued to improve the design with NEO Hi-Top—a battery that held international patents in 17 countries as well as 943 domestic and utility-model patents—and an improved New NEO Hi-Top design following the original model.
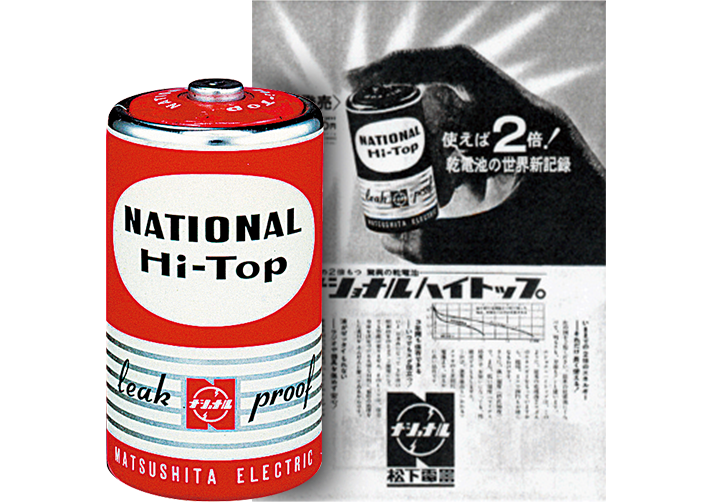
1964
Started production of SANYO “Cadnica” nickel-cadmium batteries
SANYO’s Sumoto Factory opens, and production of Cadnica nickel-cadmium batteries commences.
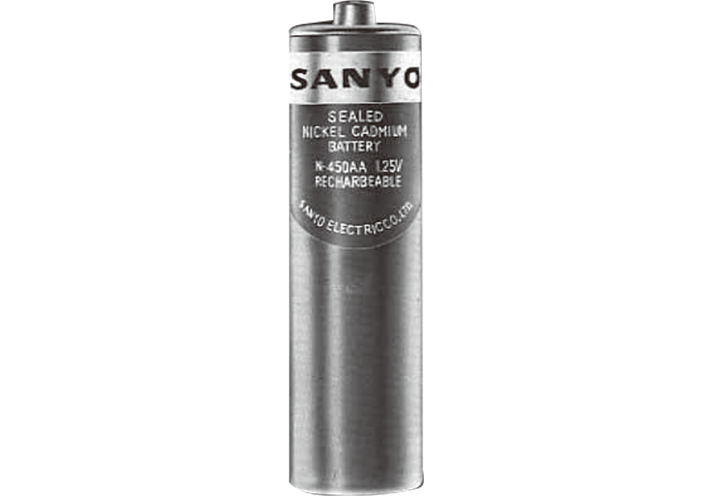
1966
Powerful battery-powered flashlights released
1967
Alkaline batteries developed and released
Image to the right shows the Alkaline Lifetime Test Trip, Travel Through the Japanese Archipelago event staged in 1968.
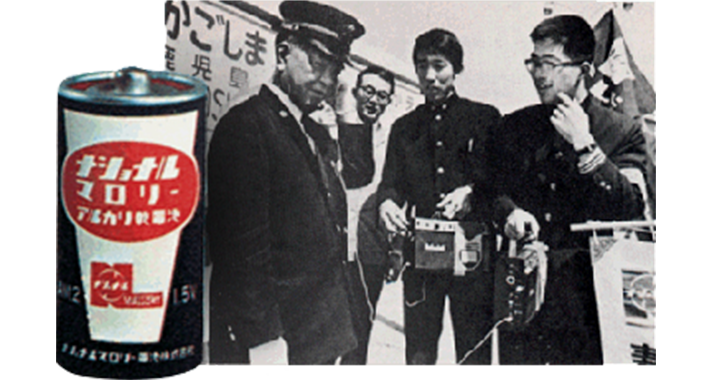
Developed first compact, sealed lead-acid batteries
1969
Released National NEO Hi-Top manganese dry batteries
Soon after the popular introduction of Hi-Top, research for a new high-performance battery with three times the capacity of Hyper and 1.5 times the capacity of Hi-Top was initiated. Conforming to international dimension standards of 6 cm height by 3.3 cm diameter, the company set a target to improve performance by 50 % over the leading battery, which was delivering double the performance of Hyper. In July 1969, the National NEO Hi-Top was released, boasting what was then the world’s longest battery lifetime. To automate and accelerate manufacturing, a high-speed production line was introduced which was capable of producing more than 600 batteries per minute. The company also expanded into miscellaneous goods, medical equipment, stationery, models, fishing goods, and gardening, supplying specialist products to meet needs specific to each industry.
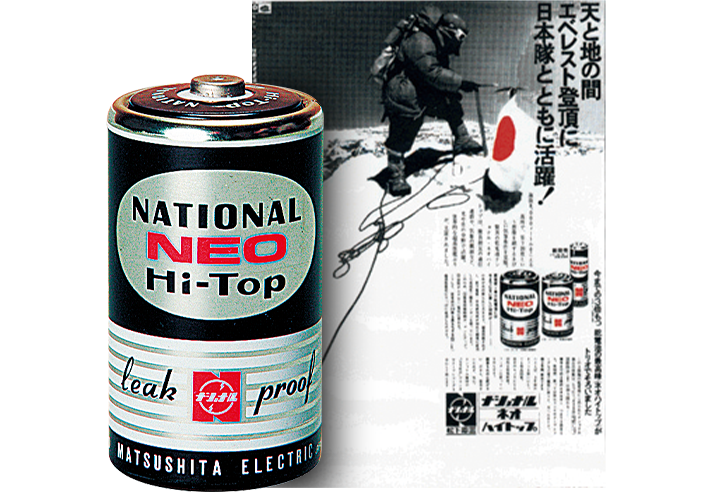
1970
Released Pananica nickel-cadmium batteries
Back in 1959, research for sealed nickel-cadmium rechargeable batteries was first initiated. Sealed nickel-cadmium rechargeable batteries were not used in Japan at that time, but the design was gaining popularity in Europe and the U.S. with unheard-of reusable performance. The first nickel-cadmium battery to see application in Japan was in 1961—a button-type design for an electric shaver. However, a quality issue forced Matsushita Electric to suspend production. Sealed nickel-cadmium batteries featured an oxygen-gas-absorbing design for protection in the event of overcharging. Development of materials such as the battery plate, separator, and electrolytic solution took place under the strictest laboratory conditions. However, in unpredictable real-life situations, the seals could be compromised due to great internal pressure, leading to battery failure. A return-type safety device was developed to address this issue after examining the structural aspects of the design. Simulating the harsh working conditions the batteries were often subjected to and “over-engineering” the structure resulted in greatly increased reliability for Pananica rechargeable batteries.

1971
Developed graphite-fluoride lithium primary batteries
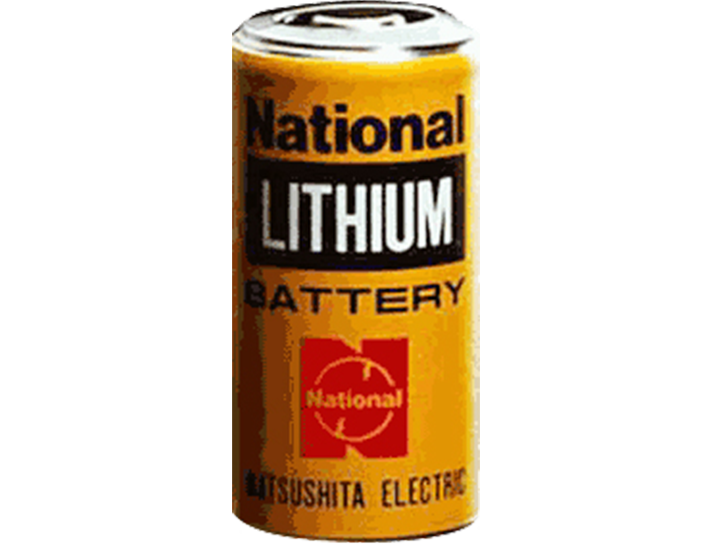
1973
Released silver-oxide batteries
Commenced production of SANYO Cadnica battery chargers
1976
Released CAREC maintenance-free automotive batteries
Around 1970, Matsushita Electric commenced development of MF (Maintenance-Free) automotive lead-acid batteries. The focus was on hybrid technology that combined a low-antimony alloy grid for the anode, an antimony-absorbable separator, and a cathode-calcium alloy grid. In the fall of 1973, CAREC (a combination of “car” and “electric”) batteries were first shipped. From 1974, as Japan’s first maintenance-free lead-acid battery, CAREC was installed in Nissan cars destined for the U.S. market. In the maintenance and repair markets, low-antimony alloy grids were used for both anode and cathode, and the resultant performance and ease of ownership made this battery a hit alternative to dry-charged batteries by the late 1970s. However, the development of an improved product—one that could hold up for 18 months with no maintenance—was initiated. At about this time, an expanded-metal grid was discovered in a negative plate of a prototype rechargeable battery that Matsushita Electric sourced from Delco Electronics Company. This led to new opportunities for the development of expanded-metal polar plates. The EXP project was initiated in 1977, and in 1980 a production line was created to manufacture the CAREC 2000 with shipments destined for automakers and repair markets. This was the product to usher in a new era in MF rechargeable battery technology.

1982
Compact LCR Series sealed lead-acid battery for video cameras developed
By 1982, as handheld video recorders grew in popularity, a need for a compact sealed lead-acid battery that could withstand rough use emerged. The company tackled the problem of improving the recovery function following over-discharge by creating a special index to quantify battery characteristics. The measurements revealed that leaving an over-discharged battery for long periods of time resulted in the worst recovery characteristics. In conventional designs, this was due to the cathode-grid alloy, but selecting a new grid material with a higher tolerance for over-discharge and overcharge solved the problem. However, the mass-production of this alloy was difficult due to its mechanical weakness when compared to traditional alloy. Later, a low-cost, high-performance alloy was developed at the Energy-Conversion Laboratory (as it was known). This was one of the major breakthroughs to drive demand for colloid lead-acid batteries.
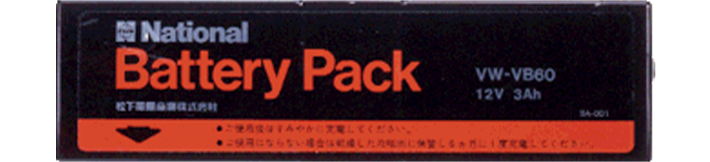
1984
BR211 released as the world’s smallest pin-type lithium battery
Lithium-carbonate rechargeable batteries developed
1985
Designed and released lithium battery pack for cameras

Developed SM Series high-capacity nickel-cadmium batteries
In 1985, cathode (SME) technology (which used a foam-like nickel substance) enabled the commercialization of a new type of Pananica battery called the SM30. Extensive manufacturing know-how was brought to bear in producing the SME plate. By filling up the foam-like nickel material with active ingredients, very high energy densities could be achieved. SME plate was also relatively easy to manufacture as no chemical reaction occurs during production, allowing for an energy- and space-efficient system. In June 1985, the first SM30 model P-100AAS entered mass production, an AA-long-type (diameter 14.5 mm x height 65 mm) with a capacity of 1,000 mAh―30 % more than existing types with a nominal capacity of 750 mAh. The weight was almost the same as existing batteries, demonstrating the highest energy density level of any cylinder-type nickel rechargeable battery in the world. The SM30 also enabled a very quick recharge time of just one hour.
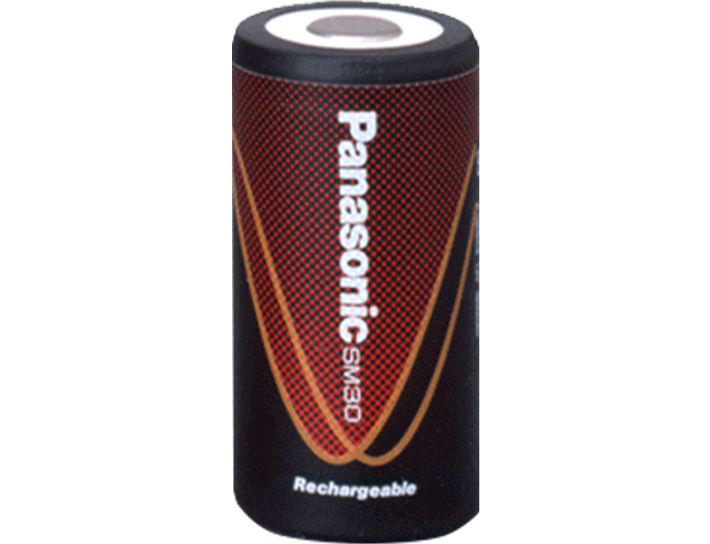
Developed copper-oxide lithium batteries
Released “CAREC ACT” automotive batteries
More than half a century had elapsed since the first car batteries entered production, and so in 1985 Matsushita Electric took the opportunity to emphasize this in its marketing for the new CAREC ACT batteries. Refilling this battery with water was unnecessary for the life of the product, with the design using a reaction mechanism that turned generated gas back into water. As well as being more convenient, the CAREC ACT eliminated liquid spills and overflows. The design was ahead of its time in terms of safety, ease of use, and ease of installation. Some of its many features included a pouch-type mat separator; a unique grid alloy developed by the company to improve charging characteristics; and equalized cell pressure in a shared-space design. The product was constructed of extremely tough, deformation-free material with additional computer-designed strengthening. Though intended for automotive use, the CAREC ACT became popular in many different roles around the world.
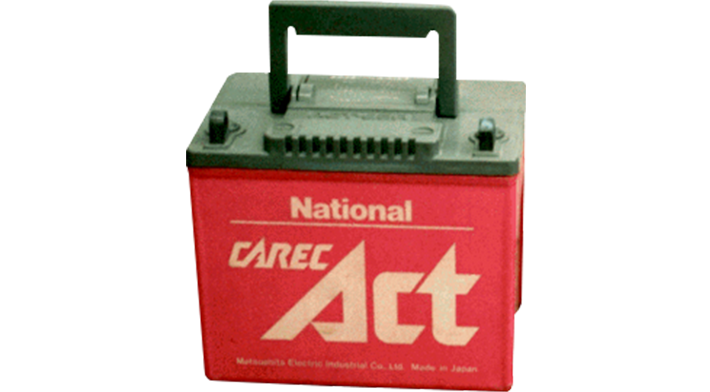
Commenced in-house production of zinc-air batteries
1986
Started production and practical application of Sun Cellums II solar batteries, a world first
Cumulative auto battery production reaches 30 million
1987
Released Ultra Alkali and Panasonic Alkali batteries
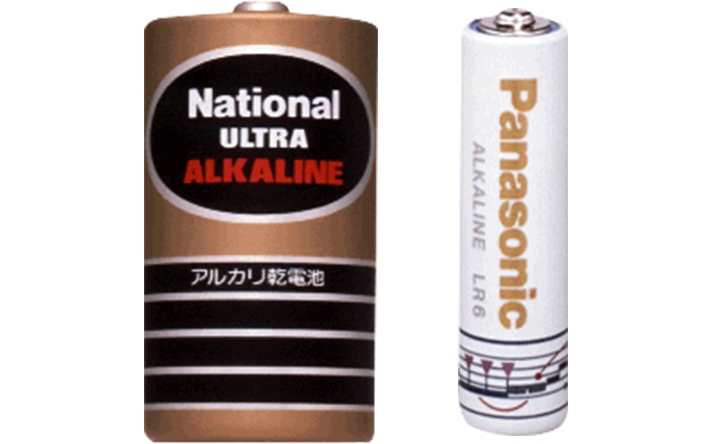
1988
Developed nickel-metal hydride batteries
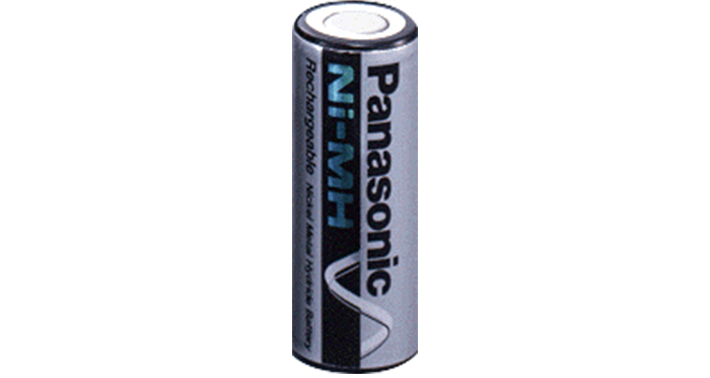
1991
Introduced mercury-free manganese batteries
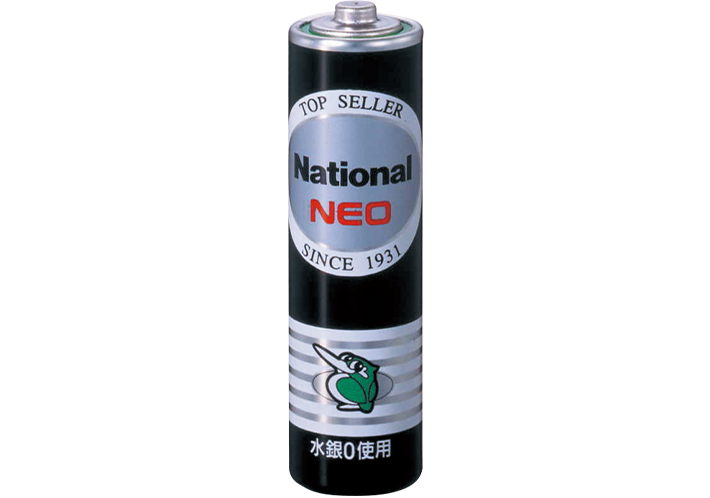
1992
Released mercury-free ALKALINE batteries

Developed nickel-metal hydride battery for Electric Vehicles (EV)
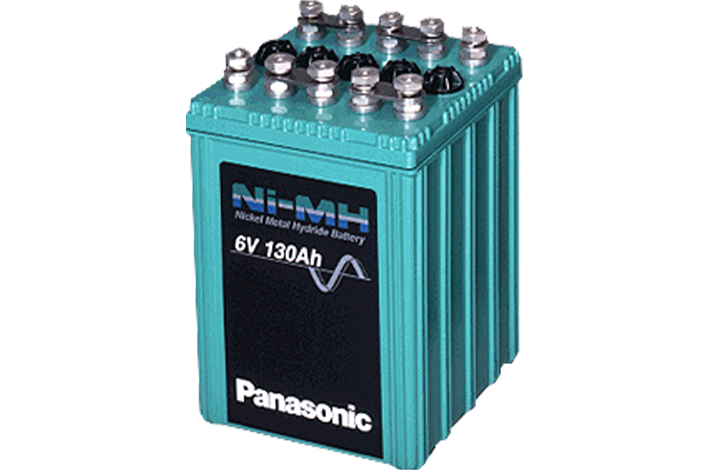
Cumulative battery production and sales total 50 billion units
SANYO installs Japan's first solar power system in a private home
1994
Developed lithium-ion rechargeable batteries

SANYO commences sales of the Residential Solar Power System
SANYO starts production of cylindrical-type lithium-ion batteries

1995
Released high-current Panasonic Alkaline batteries
Introduced Super 300 nickel-metal hydride batteries
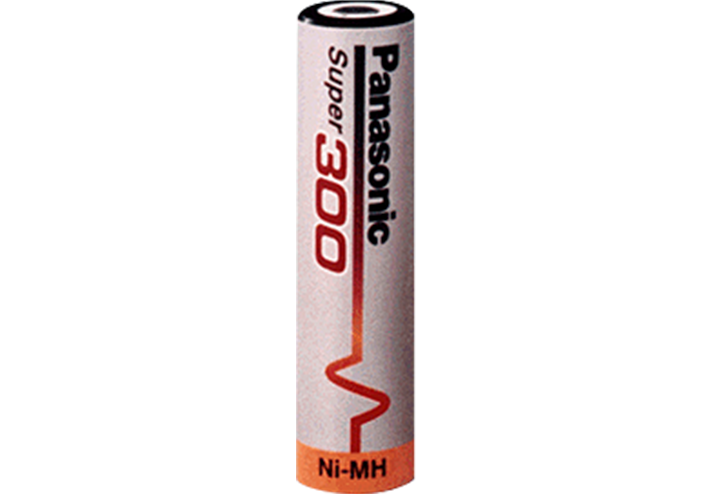
1996
Release of new Panasonic Alkaline batteries
1997
Cumulative auto battery production at Hamanako Factory surpasses 100 million
Developed Super 350 cylindrical-type nickel-metal hydride batteries
Developed nickel-metal hydride battery pack for use in hybrid cars
In a joint development with Toyota, we developed the nickel-metal hydride battery pack for hybrid electric vehicle (HEV), a car design that combines an internal combustion and an electric engine. Mass production followed. EV batteries, which are continually improving in performance, are attracting more and more attention.

Developed EV-28 nickel-metal hydride battery module for use in compact EVs
The ideal battery for electric vehicles, the compact nickel-metal hydride battery module entered production in 1997 and drove further interest in hybrid vehicles.
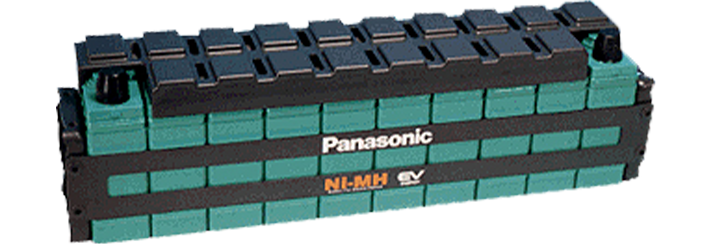
Began production of SANYO HIT* photovoltaic modules
* "HIT" is a trademark of Panasonic Group. The name "HIT" is a derivation from "Heterojunction with Intrinsic Thin Layer" which is an original technology of Panasonic Group.
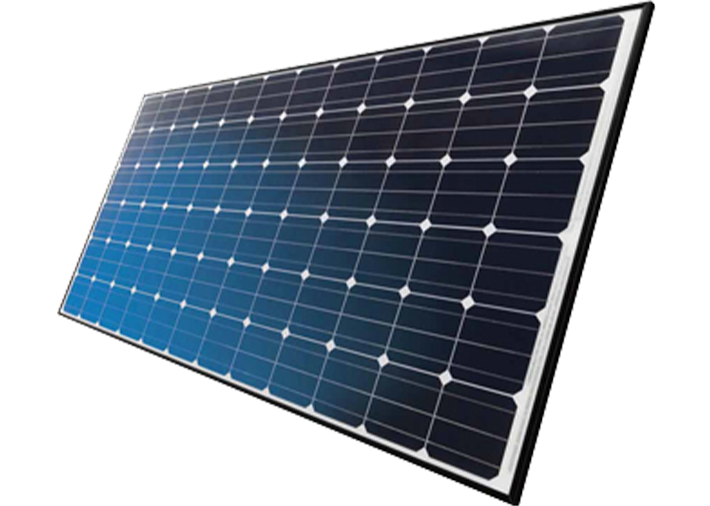
1998
Released prismatic-type lithium-ion rechargeable batteries after attaining industry-leading energy density
With industry-leading energy density, a new prismatic-type lithium-ion rechargeable battery set a high standard for notebook computer battery performance. The success of this design led to us setting up an advanced production system to meet global demand.
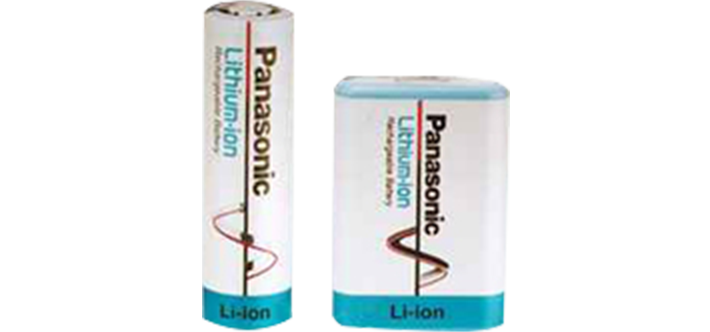
Developed paper-lithium-cell coin-type batteries
Developed high-power nickel-metal hydride batteries
Cumulative battery production and sales reaches 80 billion
1999
Cumulative carbon (battery) rod production and sales exceeds 200 billion
Top image shows carbon rod furnaces in operation circa 1901-1902
Bottom image shows carbon rods inside a furnace circa 1901-1902
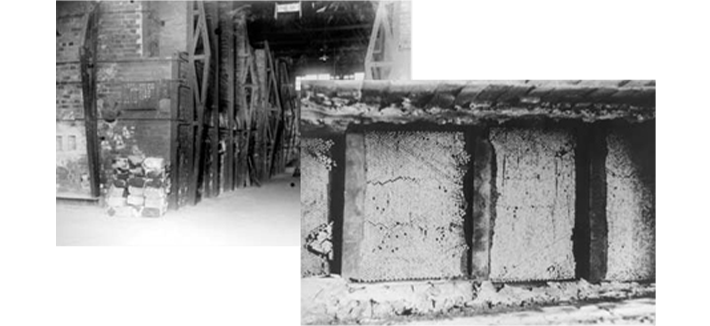
Developed paper-coin CR Series coin-type lithium batteries
Began production of SANYO lithium polymer batteries
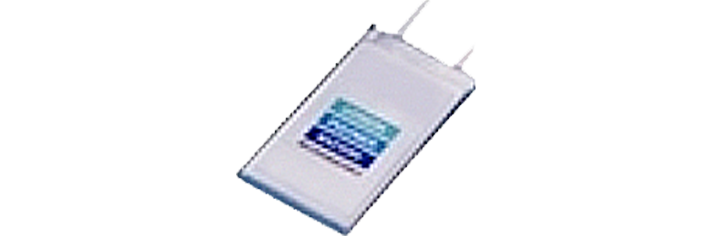
2000
Introduced a new line of AAAA nickel-metal hydride batteries
Released advanced zinc battery for EV
Created lightweight prismatic-type lithium-ion batteries
Commenced sales of world's first double-sided solar module, SANYO HIT Double
2001
Developed global-standard-sized prismatic-type lithium-ion rechargeable batteries
Cumulative domestic production of cylindrical-type lithium-ion batteries reaches one billion
Cumulative battery production and sales reaches 100 billion
SANYO completes among the world's largest photovoltaic generation systems, the Solar Ark*
* As measured on a single surface of a single building (according to in-house research)
2004
Released OXYRIDE dry battery
SANYO commences production of battery system for Ford Escape hybrid
Operations begin at new Nishikinohama plant

SANYO commences production of HEV battery module for Honda
2005
Developed industry-leading lithium-ion battery with energy density of 600 Wh/L
Jointly developed next-generation battery with Intel Corporation to support extended notebook runtime
SANYO commences eneloop sales
Operations begin at new Nishikinohama plant
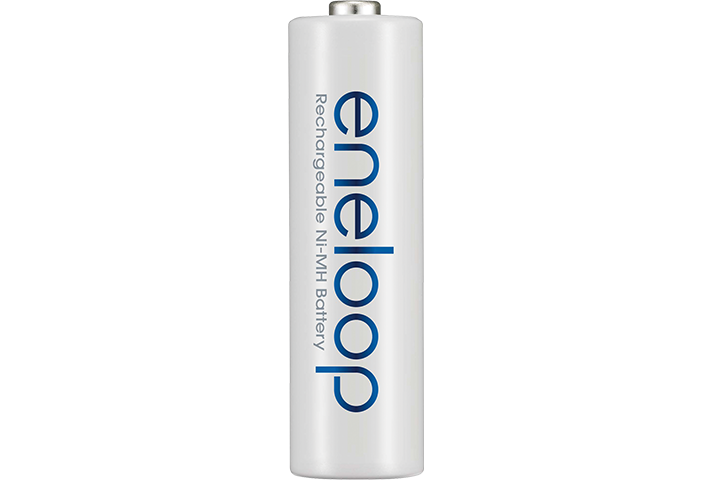
2006
Successfully miniaturized fuel battery system for mobile devices by developing a new fuel-supply method
Commenced shipping high-capacity 600 Wh/L lithium-ion batteries for notebook computers
Established industry’s first mass-production infrastructure for a safer high-capacity lithium-ion battery
2008
Released EVOLTA alkaline dry batteries
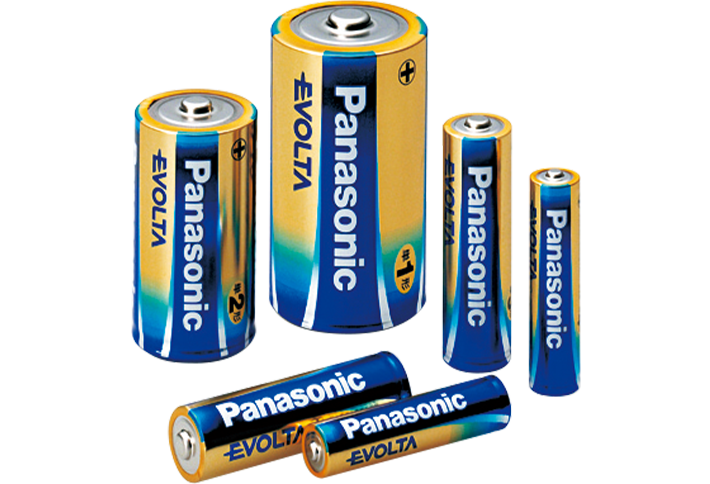
Panasonic Corporation Energy Company established
Released Rechargeable EVOLTA nickel-metal hydride batteries
2009
Developed high-energy, ultra-reliable lithium-ion battery module
Commenced production of 3.1 Ah high-capacity lithium-ion batteries
Created high-power, long-endurance direct methanol fuel cell system
2010
Introduced rechargeable EVOLTA “e” nickel-metal hydride batteries
Global cumulative battery production surpasses 150 billion
SANYO establishes lithium-ion standard battery mass production system
Initiated mass production of lithium-ion batteries for HEV at Tokushima plant Completed "Green Energy Park" in Kasai

SANYO starts mass-production of lithium-ion batteries for HEV
2013
Solar LED Lantern Debuts
Panasonic releases the multi-award-winning Solar LED Lantern, a two-piece lamp and solar panel product able to supply hours of efficient illumination in areas with no access to electricity.

2014
Panasonic eneloop goes global
Rechargeable eneloop gains global distribution via the Panasonic network and sales continue to climb as consumers recognize the benefits of low cost and high performance.

2015
Solar Storage Device Launches
Panasonic eneloop’s most advanced, cost-effective, and long-lasting solar LED light and portable device recharging solution is launched with the specific objective of bringing safe and reliable light to people without electrical access.
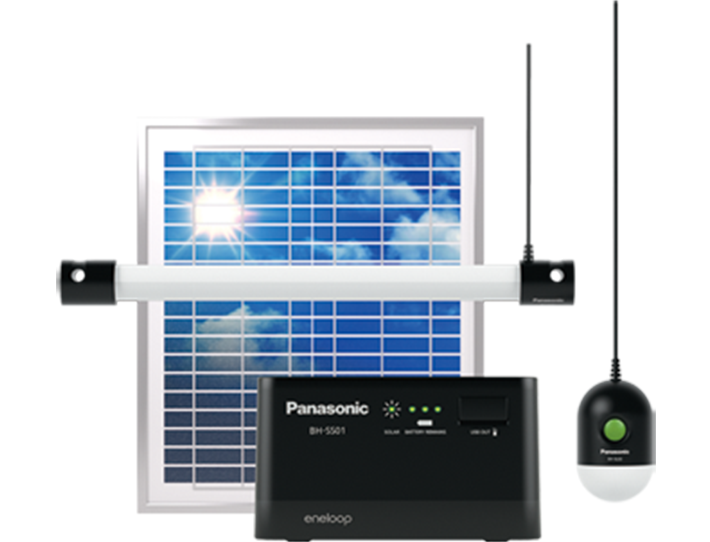
2019
Our first zero-CO2* factories on the American continent
Three factories operated by Panasonic Brazil (Co., Ltd.) in San Jose, Extrema, and Manaus become Panasonic’s first zero-CO2* factories on the American continent. The achievement was made possible through a reduction in the use of fossil fuels, the utilization of carbon credits, and the procurement of 100 % renewable electricity.

* Panasonic Group’s establishment of zero-CO2 factories means realization of net zero CO2 emissions from factory production across the world. To do so, we promote our conventional energy saving activities (e.g., switching to LED lighting), advanced energy saving technologies such as Factory Energy Management System (FEMS), productivity improvements, and innovative manufacturing. Other means include a combination of the following efforts: promoting use of renewable energy by adopting photovoltaic power systems, energy storage equipment, and hydrogen fuel cells; procuring electricity derived from 100 % renewable energy sources; and obtaining environmental values.
2020
200 billion dry batteries shipped globally
In September 2020, Panasonic became the first Japanese company to ship a cumulative total of 200 billion dry batteries globally.

Two more factories achieve zero-CO2* status
Panasonic Energy (Wuxi) Co., Ltd. (PECW) and Panasonic Centroamericana S.A. (Corp.) become zero-CO2* factories.
* Panasonic Group’s establishment of zero-CO2 factories means realization of net zero CO2 emissions from factory production across the world. To do so, we promote our conventional energy saving activities (e.g., switching to LED lighting), advanced energy saving technologies such as Factory Energy Management System (FEMS), productivity improvements, and innovative manufacturing. Other means include a combination of the following efforts: promoting use of renewable energy by adopting photovoltaic power systems, energy storage equipment, and hydrogen fuel cells; procuring electricity derived from 100 % renewable energy sources; and obtaining environmental values.
2021
Our first zero-CO2* factory in Southeast Asia
Panasonic Energy (Thailand) Co., Ltd. (PECTH) becomes our group’s first factory in Southeast Asia to achieve zero-CO2* status.

* Panasonic Group’s establishment of zero-CO2 factories means realization of net zero CO2 emissions from factory production across the world. To do so, we promote our conventional energy saving activities (e.g., switching to LED lighting), advanced energy saving technologies such as Factory Energy Management System (FEMS), productivity improvements, and innovative manufacturing. Other means include a combination of the following efforts: promoting use of renewable energy by adopting photovoltaic power systems, energy storage equipment, and hydrogen fuel cells; procuring electricity derived from 100 % renewable energy sources; and obtaining environmental values.